Yarilet Perez is an experienced multimedia journalist and fact-checker with a Master of Science in Journalism. She has worked in multiple cities covering breaking news, politics, education, and more. Her expertise is in personal finance and investing, and real estate.
Total quality management (TQM) is the continual process of detecting and reducing or eliminating errors in manufacturing. It streamlines supply chain management, improves the customer experience, and ensures that employees are up to speed with training. Total quality management aims to hold all parties involved in the production process accountable for the overall quality of the final product or service. RNA Sequencing
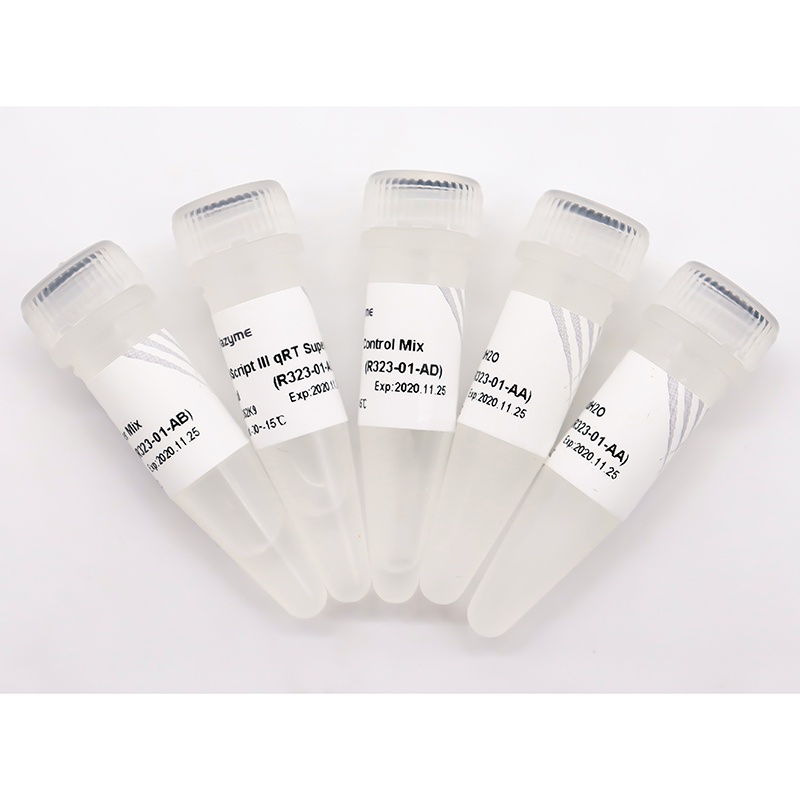
Total quality management is a structured approach to overall organizational management. The focus of the process is to improve the quality of an organization's outputs, including goods and services, through the continual improvement of internal practices. The standards set as part of the TQM approach can reflect both internal priorities and any industry standards currently in place.
Industry standards can be defined at multiple levels and may include adherence to various laws and regulations governing the operation of a particular business. Industry standards can also include the production of items to an understood norm, even if the norm is not backed by official regulations. Acceptance sampling might be used to check the progress toward the TQM goal.
Perhaps the most famous example of TQM is Toyota's implementation of the kanban system. A kanban is a physical signal that creates a chain reaction, resulting in a specific action. Toyota used this idea to implement its just-in-time (JIT) inventory process.
The company decided to keep just enough inventory on hand to fill customer orders as they were generated to make its assembly line more efficient. All parts of Toyota's assembly line are therefore assigned a physical card that has an associated inventory number.
The card is removed and moved up the supply chain right before a part is installed in a car, effectively requesting another of the same part. This allows the company to keep its inventory lean and not overstock unnecessary assets. Effective quality management resulted in better automobiles that could be produced at an affordable price.
TQM's history often dates back to the early 1900s when Walter A. Shewhart introduced modern quality control. Shewhart produced a landmark piece of industrial work entitled Economic Control of Quality of Manufactured Product in 1931. This exposition is considered one of the founding and basic principles of manufacturing quality control.
Further developments in Shewhart's work introduced new standards in quality management decades later. Joseph M. Juran published a book called What Is Total Quality Control? The Japanese Way. in 1954. The work was based on Juran's experience of being invited to Japan by Japanese scientists and engineers. Juran later co-authored Quality Planning and Analysis, another bestseller in TQM.
Another prominent figure in TQM history is W. Edwards Deming. Also posted in Japan after the Second World War, Deming became involved with the Union of Japanese Scientists and Engineers (JUSE). His career work included several TQM frameworks (Deming's 14 Points, Deming's Seven Deadly Diseases of Management, and The Deming Wheel).
The exact origin of the phrase total quality management is not known, but several parties mentioned above are credited for helping develop the general concept.
TQM is considered a customer-focused process that focuses on consistently improving business operations management. It strives to ensure that all associated employees work toward the common goals of improving product or service quality, as well as improving the procedures that are in place for production. There are several guiding principles that define TQM.
Under TQM, your customers define whether your products are high quality. Customer input is highly valued because it allows a company to better understand the needs and requirements in the manufacturing process. Customer surveys may reveal insufficient durability of goods. This input is then fed back into TQM systems to implement better raw material sourcing, manufacturing processes, and quality control procedures.
Employees must buy into the processes and system if TQM is going to be successful. This includes clearly communicating across departments and leaders what goals, expectations, needs, and constraints are in place. A company adopting TQM principles must be willing to train employees and give them sufficient resources to complete tasks successfully and on time. TQM also strives to reduce attrition and maintain knowledgeable workers.
A company should gradually evolve and strive for incremental, small improvements as it learns more about its customers, processes, and competition. This concept of continuous improvement helps a company adapt to changing market expectations. It allows for greater adaptability to different products, markets, customers, or regions. Continuous improvement also drives and widens the competitive advantage that a company has built over related companies.
TQM's systematic approach relies heavily on process flowcharts, TQM diagrams, visual action plans, and documented workflows. Every member engaged in the process must be aware and educated on their part of the process to ensure proper steps are taken at the right time of production. These processes are then continually analyzed to better understand deficiencies in the process.
A company's processes and procedures should be a direct reflection of the organization's vision, mission, and long-term plan. TQM calls for a system approach to decision making that requires that a company dedicate itself to integrating quality as its core component and making the appropriate financial investments to make that happen.
The systematic approach of TQM only works if feedback and input is given to evaluate how the process flow is moving. Management must continually rely on production, turnover, efficiency, and employee metrics to correlate the anticipated outcomes with the actual results. TQM relies heavily on documentation and planning, and only by utilizing and analyzing data can management understand if those plans are being met.
One way to utilize data is to integrate systems. TQM strategies believe systems should talk to each other, conveying useful information across departments and making smart decisions. When goods or inventory are used in one area, another department should have immediate access to that ERP information. TQM strives to allow everyone to be on the same page at the same time by linking data sources and sharing information across systems.
Data may transfer between departments freely, but there is a human element to coordinating processes and making sure an entire production line is operating efficiently. Effective communication plays a large part in TQM to motivate employees, educate members along a process, and avoid process errors whether it is normal day-to-day operations or large organizational changes.
Successful TQM requires a company-wide buy-in of every principle. The benefits of TQM quickly diminish if a company does not receive complete buy-in.
TQM is a unique process. There is not a specific formula for implementing a system that suits every business and each type of industry. But you can create a checklist of issues that might suit your enterprise and proceed with them in chronological order. Some may suit your business while others will not. Select those that you think will provide an advantage.
TQM is not a speedy process. Expect to dedicate an extended period of time to your efforts.
TQM results in a company making a product for less when it's implemented correctly. Companies that engage in TQM provide more consistent products that yield stronger customer loyalty when they emphasize quality and minimize waste.
As TQM touches every department across an organization, a company may reap substantial savings from materials sourcing, production, distribution, or back-office functions. Companies that successfully implement TQM can usually react more quickly to change and proactively plan ahead to avoid obsolescence.
A company must fully engage TQM principles to fully reap the benefits of TQM. This requires substantial buy-in from every department across an organization. This level of commitment is very difficult to achieve, requires substantial financial investment, and necessitates all levels of management to engage in TQM.
The conversion to TQM may be lengthy, and workers may feel resistant to change. A company may be required to replace processes, employees, equipment, or materials in favor of an untested, partially developed TQM plan. More skilled workers may decide to leave the company if they feel TQM processes don't appropriately utilize their skill sets.
Delivers stronger, higher quality products to customers
Results in lower company-wide costs
Minimizes waste throughout the entire production and sale process
Enables a company to become more adaptable
May require substantial financial investment to convert to TQM practices
Often requires conversion to TQM practices over a long period of time
May be met with resistance to change
Requires company-wide buy-in to be successful
TQM originated in the manufacturing sector, but its principles can be applied to a variety of industries. It provides a cohesive vision for systemic change with a focus on long-term change rather than short-term goals. TQM is used in many industries with this in mind, including but not limited to manufacturing, banking and finance, and medicine.
These techniques can be applied to all departments within an individual organization. This helps ensure that all employees are working toward the goals set forth for the company and improving function in each area. Involved departments can include administration, marketing, production, and employee training.
TQM oversees all activities and tasks that are necessary to maintain a desired level of excellence within a business and its operations. This includes the determination of a quality policy, creating and implementing quality planning and assurance, and quality control and quality improvement measures.
Various iterations of TQM have been developed, each with its own set of principles. Certain core elements persist nonetheless. These include good leadership, emphasis on quality, customer priority, error correction and improvement as an ongoing process, and job training.
A TQM diagram is a visual depiction of the business and process layout. The diagram usually shows different processes or steps, allowing management to see a process, analyze weaknesses or risks in the flow, and strategically adjust how things are done.
Total quality management is the strategic framework that encourages everyone in an organization to focus on quality improvement. The theory holds that customer satisfaction will increase by being operationally excellent. Many principles drive TQM, but the overall purpose is to eliminate errors, streamline processes, and maximize efficiency.
Toyota. "Section 4. Plant Construction and Expansion Item 4. Development and Deployment of the Toyota Production System."
American Society for Quality. "Walter A. Shewhart."
American Society for Quality. "Joseph M. Juran."
British Library. "W Edwards Deming."
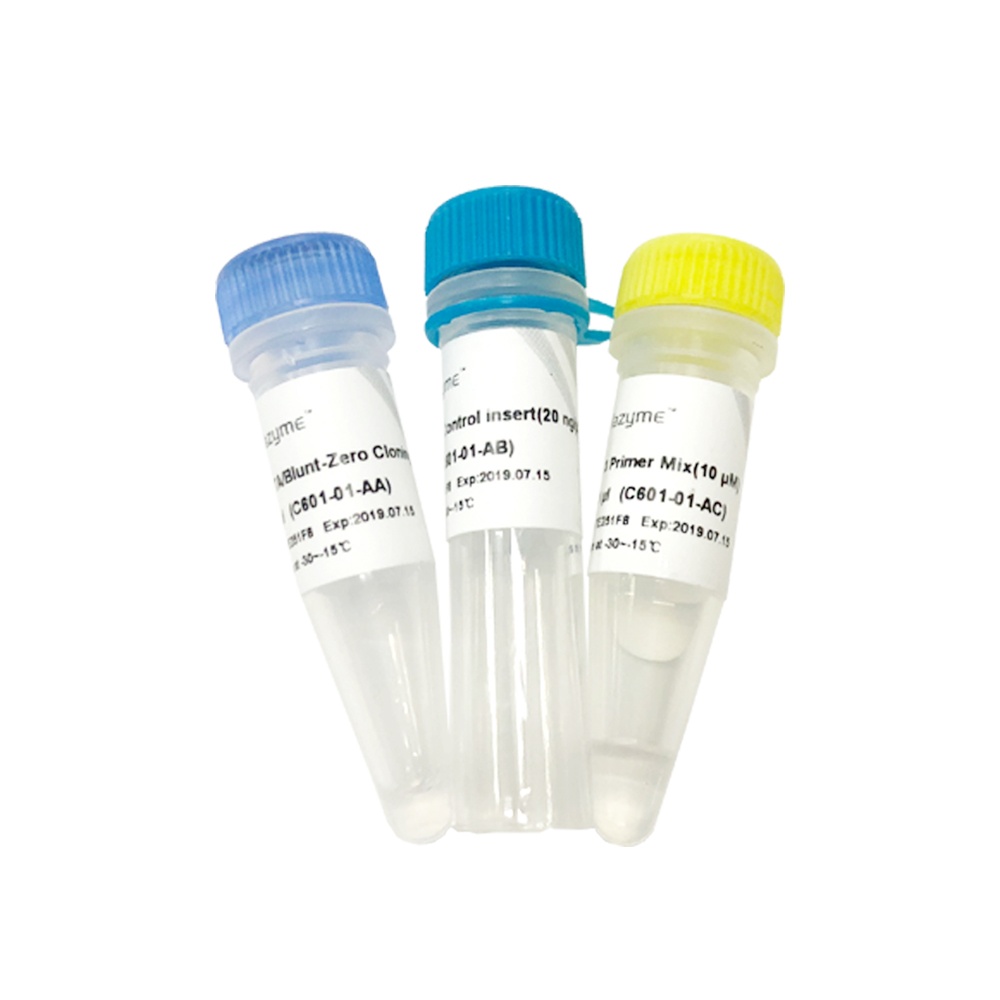
total protein quantification By clicking “Accept All Cookies”, you agree to the storing of cookies on your device to enhance site navigation, analyze site usage, and assist in our marketing efforts.